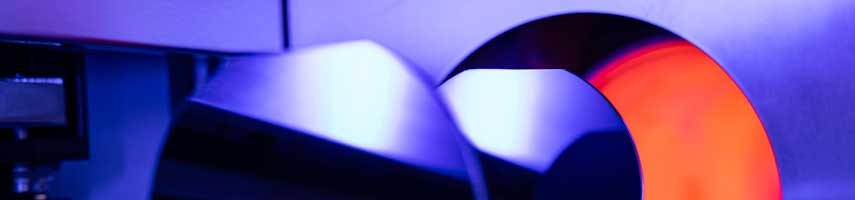
Projects
EU: Novel approaches for halogen-free and sustainable etching of silicon and glass (HaloFreeEtch)
Current industrial plasma etching processes are not sustainable because they make use of halogens. HaloFreeEtch will take a fundamental, interdisciplinary and systematic approach to find new halogen-free etching processes. HaloFreeEtch aims to identify new, halogen-free and sustainable etching processes for sustainable semiconductor manufacturing, applied to deep etching of silicon and silicon oxide. The novel etching processes we aim for shall be clean (in terms of harmful chemicals), efficient (in terms of processing speed and manufacturability) and precise (in terms of the desired shapes). HaloFreeEtch will provide a novel model- and data-based methodology for sustainability and life cycle analysis of plasma-etching to quantify the carbon-footprint of all novel etching processes. Read more about this project
Zentrales Innovationsprogramm Mittelstand (ZIM) des BMWK: Inkjet-basierte Nanoimprint-Lithographie für den Mikro- und Nanostrukturtransfer in hochbrechenden Materialien (InkNIL)
The "InkNIL" project aims to develop solvent-based inkjet inks for structure transfer using plasma etching onto high-refractive materials and substrates. Key requirements for the inks include high etching selectivity, compatibility with standard industrial print heads, and droplet stability, all influenced by the liquid's viscosity and surface tension. A closed layer with a thickness of no more than 200 nm (ideally 100 nm) is crucial for nanoimprint applications. The inkjet process allows for spatially selective application, enabling the creation of varying material heights through advanced overprinting techniques. Read more about this project
DFG-SPP: Nanomaterial-based platform electronics for PUF circuits with extended entropy sources (NanoSec2)
We investigate NanoMaterial (NM) based Physical Unclonable Functions (PUFs) with enhanced properties. We will study different technological approach to enhance entropy aiming stable multibit states of PUF-cells. Moreover, we will explore configurable CNT-FET circuits with cell selective erasability option. Building upon our previous works on non-invasive attacks against CNT-based PUFs, we will also test the resilience of the constructed CNT-PUFs against side-channel and fault-injection attacks. Read more about this project
SAB: ESF Plus Nachwuchsforschungsgruppe WiProFlex - Übertragbare wissensbasierte Prozessmodelle für eine flexible Fertigung
The aim of the interdisciplinary ESF Plus junior research group WiProFlex is the development of knowledge-based process models for flexible manufacturing processes by linking data-based methods with process-specific physics and expert knowledge as well as simulations. In order to develop reliable process models even with small amounts of data, WiProFlex develops improved data science tools and suitable data infrastructures to develop these models in hybrid approaches. Read more about this project
EU: Automated monitoring of horticulture by spectral analysis with quantum dot detectors and high-resolution optical - HORTIQD
HortiQD aims to develop an affordable machine vision system for precision farming, specialized in horticulture. We will build a hyperspectral short-wave infrared (SWIR) camera working in the wavelength range of 1 to 2 µm. The sensory system will be used directly on the field, as in-vivo measurement, as either a handheld solution or attached to an autonomously driving tractor to allow for intensive monitoring of the crop. Read more about this project
SAB: Technologieplattform für innovative, kompakte und vollintegrierte System in Package - KoVoPack
In the joint project, processes and systems as well as demonstrators for a technological platform are being developed. This platform makes it possible to produce fully integrated and compact system-in-package solutions in the optical, RF and radar application areas. In the above-mentioned areas of application, there is a need to significantly improve the functional parameters of the hardware used and to produce highly compact, compact solutions in the smallest of spaces. This requires the integration of new materials and substrates and the use of new composite techniques. At the same time, compatibility with existing CMOS production, production of SAW RF components, as well as environmental compatibility and conservation of resources must be ensured. Read more about this project
SAB: Miniaturisiertes modulares digitales 3D+-Sensorsystem mit optimierter AVT für die intelligente Zustandsüberwachung – MIMODI-3D+
With new approaches in sensor technology, packaging and connection technology, as well as data acquisition and processing, the MIMODI project can make a significant contribution to improving predictive condition and process monitoring on highly dynamic systems. In cooperation, the project partners AMAC, viimagic, ZfM and ENAS are developing a particularly small, thin and yet sensitive MEMS as a sensor element for a broadband (20 kHz) vibration sensor with significantly improved performance parameters compared to the state of the art. Read more about this project
BMBF: Optomechanische Detektion kleinster Bewegungsamplituden für hochpräzise mikroelektromechanische (MEMS) Inertialsensoren – OptoMEMS
In this project, the precise detection of the smallest movements in MEMS inertial sensors is to be significantly improved by detection approaches based on optical wave effects. In the case of gyroscopes in particular, solutions based on integrated photonic components are expected to receive a significant boost in development, to which the project partners intend to contribute with theoretical and technological preliminary work.The aim is to investigate an innovative optomechanical coupling of optical resonators with MEMS resonators and to investigate it with regard to the theoretical and actually achievable performance (sensitivity). Read more about this project
Zentrales Innovationsprogramm Mittelstand (ZIM) des BMWK: Induktives Zünden reaktiver Multilagenstapel für Fügeanwendungen auf Chip- und Komponentenebene - Indu2React
Heterogeneous integration plays a leading role in microtechnology at all levels. The use of advanced packaging technologies is key to semiconductor innovation and achieving system performance. Packaging optimization can increase functionality and performance while reducing costs. Key to this are new selective heating processes such as reactive bonding, which can locally limit or reduce the process temperature. In reactive bonding based on integrated reactive multilayer systems (iRMS), the energy to bond two components is generated by the iRMS itself. However, transferring the process to industrial applications is challenging due to the initiation of the self-propagating exothermic reaction (SER). By developing an inductive ignition process and transferring it to commercially available tools for volume production, a wide range of applications can be opened up. Read more about this project
DFG: Near-field Enhanced Optomechanical NAnoresonators – NEONA
The aim of the NEONA project is the realization as well as the investigation of the inherent physical properties of DNA-assembled strongly near-field coupled plasmomechanical nanoresonators. In this context, Au-based double-resonant plasmonic nanostructures with individual sizes of less than 450 nm and critical dimensions of less than 10 nm are envisioned. Based on the targeted optical excitation of high-frequency coherent acoustic vibrations within the nanoresonator and the associated modulation of the interparticle near-field coupling, a significantly enhanced spectral modulation of the inherent hybridized LSPR will be achieved. Moreover, a topographic approach is envisioned to selectively immobilize these hybrid nanostructures, aligned and in regular lattice structures, on an optimized pre-patterned semiconductor substrate. In this way, high density meta-surfaces consisting of all-optical (NIR) high-frequency signal generators are to be obtained. Read more about this project
AIF/ZIM: Anlagentechnik zur automatisierten elektrochemischen Abscheidung von reaktiven Materialsystemen für neue Raumtemperatur-Fügeverfahren - AnelisA
The main goal of the project is to utilize reactive multilayer systems (RMS) for different applications using electroplating. Therefore, an automated deposition tool will be constructed to achieve uniform and reproducible layer deposition. Palladium and Tin will be stacked from to different electrolytes to build up the RMS. The RMS will be used for long-term storage experiments as well as joining experiments. Read more about this project
Industrielle Gemeinschaftsforschung (IGF): Induktives Sinterwerkzeug für den Multi-Die-Attach leistungselektronischer Komponenten - InduMDA
Power modules are important components, for instance, in electric drives or converters for energy systems. To meet the increasing demands of the electronics industry for performance and miniaturization in combination with new materials such as SiC or GaN, continuous developments in heat dissipation, electrical conductivity and ampacity are required. Packaging technologies, especially between die and substrate (die attach), play a major role. Therefore, the goal is to develop an inductive sintering process at chip level that, in contrast to convective particle sintering, allows components to be bonded without global heating at low pressure application and in a short process time. A similar technology for single die sintering has already been developed in the preliminary project InSight. The goal of InduMDA is to transfer these findings to an industrially relevant multi-die sintering process. The sub-steps to achieve this goal are the development of an inductive sintering tool, the optimization of the paste to increase the efficiency of the inductive sintering process, and the adaptation as well as optimization of the existing process conditions to the multi-die setup. The research project will provide a novel heating and bonding process in the rapidly growing field of particle sintering to numerous small and medium-sized German companies from the relevant value-added stages of raw materials, systems, equipment, application and integration in the fields of power electronics, microelectronics, microsystems technology and mechanical engineering. Read more about this project
BMWK-DLR / IGF: Aluminium-Pillars als neues Material im Advanced Packaging - AlPacka
This project aims to achieve Aluminum pillar bonding using ultrasonic Flip Chip bonding. The process includes the electroplating of Al pillars and its simulation. Furthermore, the bonding process will be simulated regarding the pressure deviation for different design to gain a better understanding of the main influencing factors at different designs. Utilizing simulations at different stages, the electrode design can be optimized prior actual wafer fabrication. The goal is to demonstrate the bonding of different devices using the Al pillars. Read more about this project
DFG: Analog High-Frequency Integrated Circuits based on Carbon Nanotube Field-Effect Transistors (ICCNT)
While Carbon Nanotube devices emerge advanced performance states in research, within this project truly integrated analog high frequency (HF) circuits as well as HF subsystems based on CNTFETs will be realized and studied for the first time. HF circuit units will be designed and fabricated on the basis of the 130 nm CMOS technology node following a heterogeneous integration approach on wafer-level. Technology development and circuit design effort will be supported by extensive device simulation and compact modelling as well as electrical and physical device characterization. Read more about this project
EU: GREENER - Single Photon source and detector based on novel materials for the detection of endocrine disruptors
Drinking water is one of the most important natural resources on earth. Contaminants such as hormones therefore pose a high health risk and can affect humans and animals even at extremely low concentrations. The EU-funded GREENER project aims to develop a ready-to-use, compact and robust spectrometer with extremely high sensitivity for measuring contaminant concentrations in the (sub)ng/L range. The target is to develop novel single photon sources based on quantum dots and DNA origami and to build more efficient detectors in the near-infrared wavelength range. The modular spectrometer system based on these components will enable water safety monitoring for endocrine disrupting contaminants for (but not limited to) fisheries and aquaponics without additional infrastructure and trained personnel. Read more about this project
Zentrales Innovationsprogramm Mittelstand (ZIM) des BMWK: TraDruMa - Transparente Druckmesssensormatrix zur gleichzeitigen Bestimmung der Form / Geometrie und des Drucks eines Fußes beim Stehen und Gehen
The planned project aims to develop a transparent pressure sensor matrix that allows for the optical capture of foot geometry from below using 2D camera technology. The sensors will be manufactured using innovative printing technology and are designed to capture both static and dynamic loads. This enables more precise patient care, such as with insoles, and prevents misloads. The development of transparent sensors and conductors is crucial, which will be applied to foil to measure the pressure distribution on the foot. Read more about this project
DFG: Gasspektrometer Thema „Mobiles emissionsbasiertes Mikrospektrometer zur Analyse unbekannter gasförmiger Substanzen“
Ein neuartiges mobiles emissionsbasiertes Mikrospektrometer zu Analyse gasförmiger Substanzen ist Gegenstand dieses Projektes. Anders als bei konventionellen Gassensoren, welche in der Regel auf die Konzentrationsmessung vorab spezifizierter Gase beschränkt sind, kann das aufzubauende System, Gase gänzlich unbekannter Zusammensetzungen analysieren und die Konzentration der enthaltenen Bestandteile bestimmen. Read more about this project